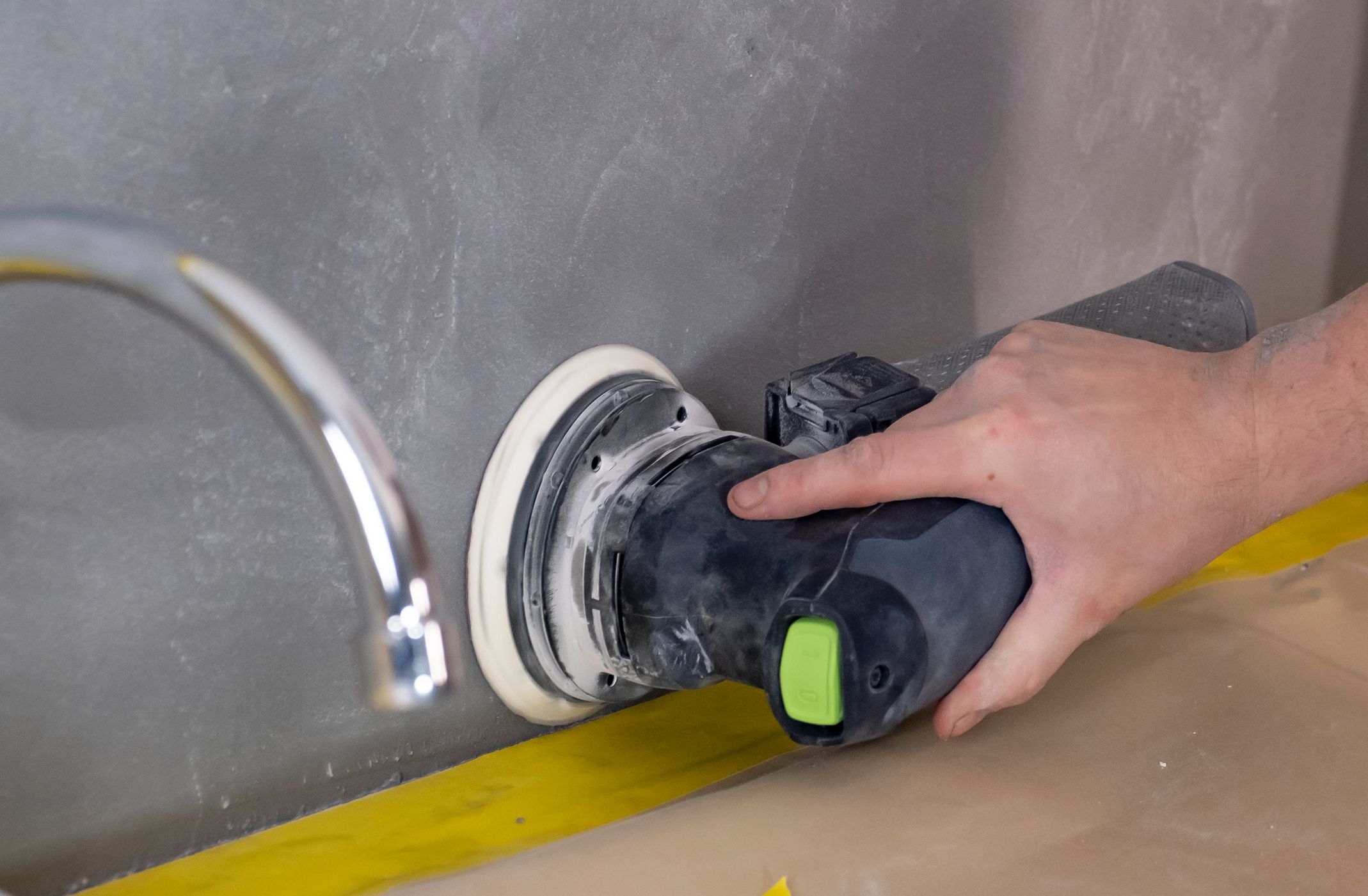
Disco para lixar concreto: como escolher e utilizar
Deseja descobrir qual é o melhor disco para concreto e como fazer a melhor escolha? Confira este conteúdo!
Por Fábio Freitas, Especialista em Ferramentas Abrasivas
A nossa civilização evoluiu muito desde o uso das primeiras ferramentas de pedra lascada e depois de pedra polida que eram usadas para caçar, triturar e cortar seus alimentos. Esta fase da Idade da Pedra abriu caminho posteriormente para o que chamamos de Idade dos Metais cuja principal consequência foi pavimentar o caminho para o surgimento das primeiras civilizações da Antiguidade.
A idade dos Metais começou por volta do ano 6000 aC, logo após o período Neolítico quando os grupos que eram nômades se tornaram sedentários graças à agricultura. As aldeias agrícolas se transformaram em cidades por mérito do êxito nas colheitas e do aumento populacional. Os instrumentos de pedra, tão úteis para os hominídeos nos primeiros períodos pré-históricos, foram substituídos por outros feitos de metal. O fogo ganhava uma nova utilidade: fundir e modelar o metal.
O primeiro metal a ser trabalhado foi o cobre. Com o passar do tempo, outros tipos de metais foram utilizados, como o bronze e o ferro. Os instrumentos de metal foram então empregados como armas de guerra e no trabalho cotidiano, como a caça, a pesca e na prática agrícola. O trabalho, a partir daí, tornava-se mais eficiente.
Neste período da idade dos Metais, migramos do uso do Cobre como metal inicialmente utilizado para o bronze quando os artesãos buscavam fabricar instrumentos mais resistentes. O bronze é mais rígido e resistente que o cobre e permitiu a confecção de instrumentos que resistissem ao tempo e garantissem a segurança aos grupos em guerra com seus inimigos. O ferro foi o último tipo de metal utilizado pelos hominídeos durante a pré-história e tal qual os outros metais, ele foi utilizado na fabricação de ferramentas e armas de guerra. Para se obter o ferro, era necessária sua fundição, remoção de impurezas e regulação da quantidade de carbono para daí ser moldado conforme o objetivo dos artesãos.
A idade dos metais abre um capítulo fundamental da nossa história: o da Metalurgia[2], que é o conjunto de processos e técnicas para extração, fabricação, fundição e tratamento dos metais e suas ligas.
Na Metalurgia, a fundição é o processo de colocar metal líquido em um molde, que contém uma cavidade com a forma desejada, e depois permitir que ele resfrie e solidifique. A parte solidificada é conhecida como peça fundida que daí deve ser retirada do molde para passar por uma série de processos até que esteja acabada. A fundição é a técnica mais frequentemente utilizada para fazer peças complexas que seriam difíceis ou mais caras de fazer por outros métodos.
A primeira etapa do processo de fundição [3] é a preparação dos moldes que são feitos com areias específicas e resinas sintéticas. É através do molde, que o metal fundido irá fluir e solidificar até atingir o formato final da peça fundida. Na fabricação dos moldes, alguns elementos como os drenos ou canais de vazamento, que são importantes para que quando o metal fundido preencher as cavidades, o ar e possíveis contaminações sejam expulsos.
Figura 1: Injeção do metal fundido no molde de areia[4]
A etapa de resfriamento e solidificação é muito crítica no processo de fundição já que um esfriamento excessivamente rápido provoca tensões mecânicas na peça, inclusive com o aparecimento de trincas e formação de bolhas. Se houver um resfriamento lento, também haverá diminuição da produtividade da linha de produção. Estes eventos de resfriamento também afetam bastante o tamanho, a forma, uniformidade e composição química dos grãos formados na peça fundida, que por sua vez influencia suas propriedades globais como a sua resistência mecânica.
Após resfriada, a peça é desmoldada, o que é feito com a remoção da areia que a envolve por fora e nas cavidades. Essa remoção é feita mecanicamente com a remoção grosseira do maior volume e logo após isso, a peça entra no processo de jateamento, no qual irá receber um jato de granalha, mais comumente de aço, para remoção da areia que fica impregnada em sua superfície.
Pronto, daí entramos na etapa de rebarbação! Esta operação se faz necessária pois a peça fundida possui diversas rebarbas, como mostradas na figura abaixo, próxima à linha de partição dos moldes, canais, massalotes, drenos, marcações e descontinuidades das partes que compõem os moldes. As peças leves serão colocadas em esteiras de acabamento e passarão por diversas estações de rebarbação. Peças mais pesadas são levadas às estações de rebarbação com o uso de empilhadeiras.
Figura 2: Rebarbas em peças fundidas [5]
É na etapa de rebarbação que fazemos o uso de diversos produtos abrasivos como lixas, discos de corte e desbaste, rebolos convencionais e diamantados que são utilizados de maneiras diferentes, a depender da criticidade da peça.
Peças fundidas para aplicações mecânicas dificilmente ficam prontas e acabadas após a limpeza e rebarbação. Pos isso, elas ainda necessitam passar por alguns tratamentos por outras máquinas-ferramentas até chegarem ao seu destino final. As peças que serão utilizadas em aplicações de precisão poderão passar por usinagem (tornamento, fresamento), tratamento térmico para melhoria de propriedades mecânicas e prologamento de sua vida útil, e também pela retificação de precisão com o objetvo de se atingir geometria e rugosidade superficial adequadas à especificação final. No entanto, há peças que ao saírem da fundição e do jateamento, já estão prontas e acabadas, não necessitando as vezes passar pela rebarbação.
Bom, mas de tudo o que sabemos sobre as fundições, nosso interesse maior, é claro, está nas ferramentas abrasivas. O DNA da Norton é o de entregar conhecimento e as melhores soluções para que os processos de rebarbação possam ser executados com alta produtividade e segurança. Afinal, uma ferramenta abrasiva, quando mal utilizada pode se tornar uma arma muitas vezes letal.
Aqui na Norton, considerando que a peça fundida seja feita de ferro fundido, nodular ou cinzento, classificamos o processo de rebarbação conforme mostramos na figura abaixo.
Figura 3: Esquema de processos de acabamento de peças de ferro fundido com ferramentas abrasivas[6]
Como podemos ver, temos os seguintes processos:
Figura 5: Rebarbação pendular de peça fundida [8]
Figura 6: Rebarbadora Norton com rebolo diamantado para operação a 100 m/s. [9]
No Brasil, a partir de 2010, cada vez mais observa-se a instalação de células de acabamento automatizado e um dos grandes avanços tecnológicos que permitiu o crescimento dessa oferta de rebarbação automatizada é o desenvolvimento de rebolos diamantados de alta performance que cada vez mais são utilizados em rebarbação de ferro fundido. Células de acabamento automatizado operam em altíssima produtividade, oferecem mais qualidade ao processo de rebarbação e principalmente eliminam alguns riscos de segurança que existem nas operações realizadas manualmente. Este tipo de acabamento pode ser dividido em duas frentes:
Nas fundições, o trabalho e as movimentações pesadas no processo fabril expõem os operadores à vários riscos de segurança. Na rebarbação, por exemplo, aquelas que envolvem diretamente o uso da ferramenta por um operador de rebarbação são as mais críticas. Isto é corroborado pelos dados de prevalência de CAT (Comunicação de Acidente de Trabalho) do Observatório de Segurança e Saúde no trabalho[10], que mostram que entre 2012 a 2020, no setor das fundições, cerca de 38% dos CAT’s abertos estão relacionados à escoriações e ferimentos superficiais causados por abrasão. A mesma análise, porém, com foco nas ocupações no mesmo setor, demonstra que o profissional envolvido na rebarbação de metal e o alimentador da linha de produção, respondem por 31% e 13% das notificações, respectivamente. Diante de números dessa magnitude, torna-se fundamental o contínuo aperfeiçoamento do processo produtivo com constante investimento em automação.
Além disso, vale ressaltar que a qualificação das equipes de rebarbação e manutenção de máquinas por meio de treinamento é de grande importância, pois a maioria absoluta dos acidentes com ferramentas abrasivas está relacionada ao não cumprimento das normas e recomendações de montagem e uso, contidas no rótulo da própria ferramenta. Como dito anteriormente, um disco de corte ou até mesmo um rebolo, quando são mal utilizados, podem levar a acidentes fatais.
Para aprender mais sobre segurança no uso de ferramentas abrasivas, a Norton oferece conteúdos gratuitos na plataforma Norton Academy como o curso de Noções básicas sobre ferramentas abrasivas e com o curso de Segurança no uso de discos de Corte e Desbaste.
Bibliografia
[1] – Por Carlos César Higa- https://brasilescola.uol.com.br/historiag/idade-metais.htm – acessado em 5/9/22
[2] – https://pt.wikipedia.org/wiki/Metalurgia – acessado em 5/9/22
[3] – https://pt.wikipedia.org/wiki/Fundi%C3%A7%C3%A3o – acessado em 5/9/22
[4] – https://www.revistaferramental.com.br/artigo/fundicao-o-que-e-e-como-funciona/
[5] – BRAGA JR, ARNALDO FERREIRA – II Workshop LABMAT da área de fundição – Defeitos em peças fabricadas pelo processo de fundição – http://www.jmmsassessoria.com.br/upload/files/defeitos-em-pecas-fabricadas-pelo-processo-de-fundicao.pdf – acessado em 5/9/22
[6] – Arquivo interno Norton Abrasivos – adaptado de apresentação corporativa, 2021
[7] – Figura adaptada – origem: http://metalurgicasoares.com.br/ – acessado em 5/9/22
[8] – Figura adaptada – origem: linkedin do autor
[9] – Arquivo interno Norton Abrasivos – adaptado de apresentação corporativa, 2021
[10] – https://smartlabbr.org/sst/localidade/0?dimensao=prevalenciaAcidentes – acessado em 5/0/22
[11] – https://cursos.nortonacademy.com.br/todos